Strengthen your Lean Six Sigma expertise by obtaining a Green Belt certification
As well as providing a basic knowledge of Lean and Six Sigma, and practical tools and techniques for achieving improvements in an organisation, the Green Belt Lean Six Sigma training course will focus on putting these into practice. The aim is to enable participants to become active players in such optimisation projects.
Training type: Open classroom and In-Company
Timing: 6 days + 1 certification day
This training will enable you to:
Pedagogical approach
Over six days, the course combines presentations of concepts, discussions, and experience-sharing, with many practical exercises and applications to a case study. A business game illustrates practical application. A comprehensive toolbox of techniques and methods is provided that can be immediately applied in practice. The learning outcomes are regularly assessed through a quiz.
From the start of the training, each participant works on their own case, to be carried out independently outside of class time, but with feedback from the trainer at regular intervals during the training sessions. The case is presented to a panel of judges during the certification process.
Content
This training is aimed for:
Prerequisites required: Lean Six Sigma Yellow Belt, Preferably experience in process modelling
Certification
The certification process consists of two parts:
Typical program
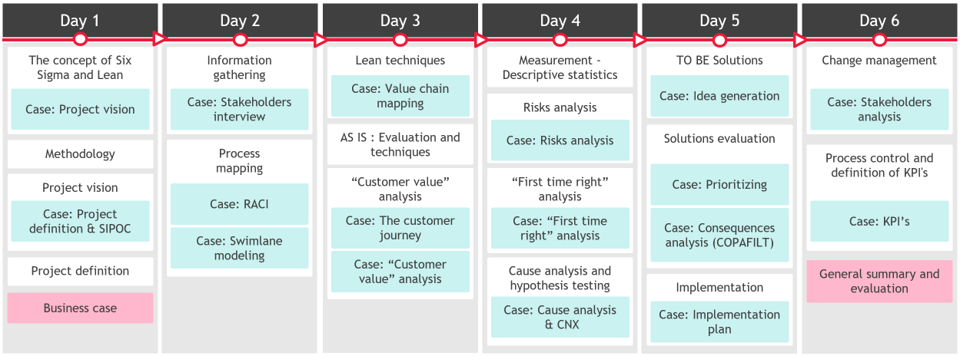